We provide high quality pallets to meet your demands
We ensure a seamless automated flow
We keep your automated lines going
Ensuring seamless automation with IPP's high-quality pallets
Automation systems depend on pallets that meet stringent standards for consistency and durability to ensure seamless operations. Any deviations or defects in pallet quality can disrupt automated workflows, leading to costly delays and inefficiencies. High-quality pallets are essential for maintaining the smooth and continuous movement of goods through automated systems, which operate around the clock to meet the relentless demands of modern supply chains.
Automation in warehouses and production lines comes with numerous challenges, and one of the most critical requirements is preventing disruption. Even with robots, computers, and smart software controlling operations, a damaged pallet can still interrupt the meticulously organised processes.
At IPP, we recognise the importance of maintaining a smooth flow in automated environments. Our One-Way Trip service ensures that our pallets consistently meet the highest standards required for automation. Each pallet undergoes thorough inspection and quality control before being dispatched to our customers. This meticulous attention to detail is part of our commitment to delivering a seamless automated flow, ensuring your operations remain uninterrupted and efficient.
Do you think about the quality of your pallets when working within an automated environment?
Pallet quality is an important consideration when automating a warehouse, as a poor-quality pallet can easily disrupt the entire process. Learn more about the insights of running an automated warehouse related to pallet quality - from the point of view of different stakeholders - including the warehouse equipment manufacturer and the user of an automated warehouse – to understand how IPP ensures delivery of the best pallet quality for a seamless flow in an automated warehouse.
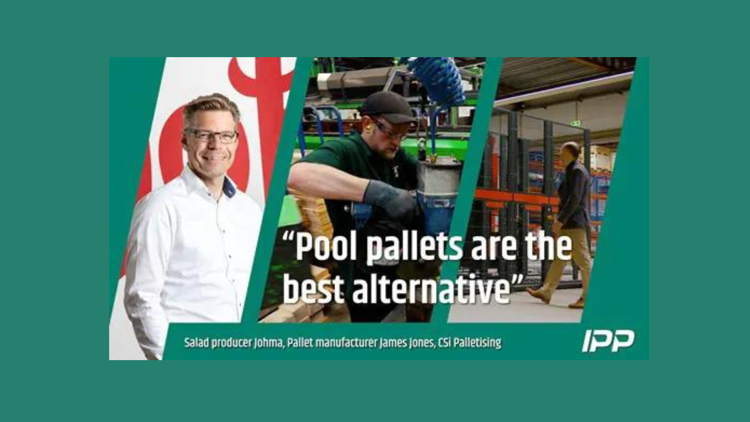
Johma has also invested in warehouse automation and recognizes the challenges
An automated warehouse has big advantages, but is very sensitive to disruptions. And few things are more disruptive than broken pallets. We really want to avoid those. The best way to avoid this would be to buy new pallets for each delivery, but this is simply not practical or cost-effective, which is why pooled pallets provide the best alternative. - Remco Rijsenbrij, Directeur Operaties Johma
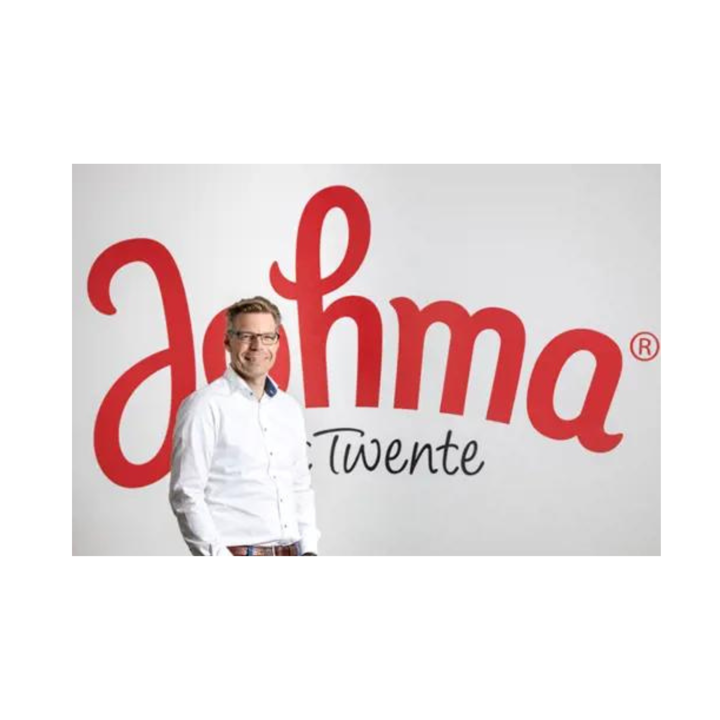
Do you need quality pallets to ensure efficient and effective automated lines?
High-quality pallets are essential to keep automated warehouse lines flowing and the IPP One Way Trip service guarantees the best pallet quality. After every trip, a pallet returns to an IPP depot for a thorough inspection and is repaired if needed to keep the pallet up to specification. High-quality pallets are designed to meet the rigorous demands of automation, ensuring reliable performance and minimising the risk of downtime. Thus, investing in quality pallets from IPP is essential for optimising the efficiency and effectiveness of automated lines in warehouses and production facilities.
Interested in learning more about how we keep our pallets in great shape? Watch the video of our Bardon Hill depot in the UK.
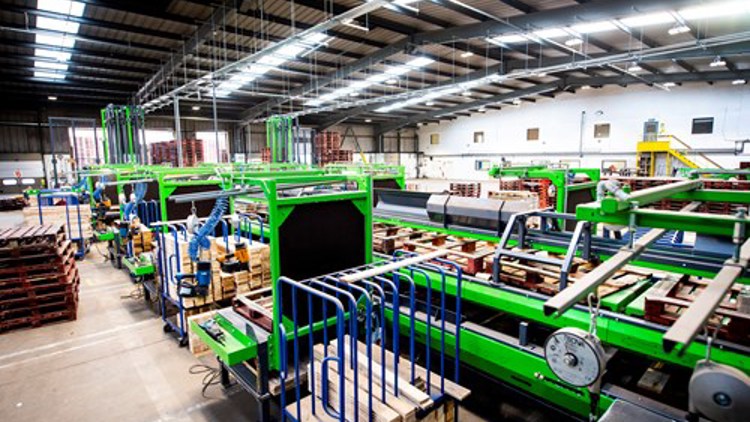
Seamless automated flow at CSi Palletising?
We visited CSi Palletising, an internationally-renowned company offering fully-integrated material handling and pallet pool systems for the FMCG/CPG industry. There we learned more from their perspective about warehouse automation and the importance of pallet quality. Watch the video to find out more.
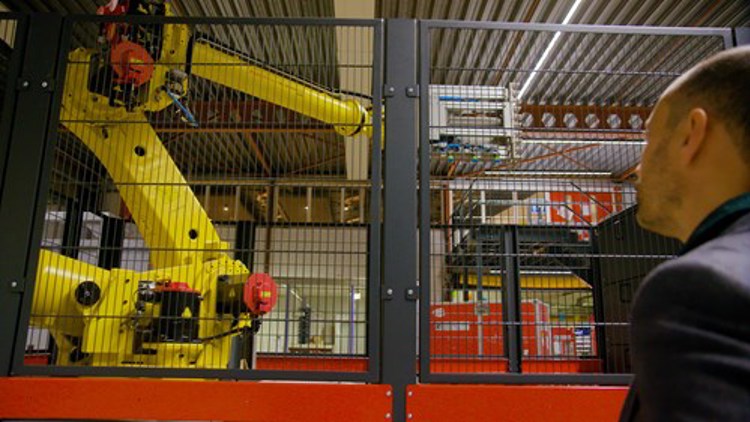
Do you need quality pallets to ensure an efficient automated flow?
It's up to you.
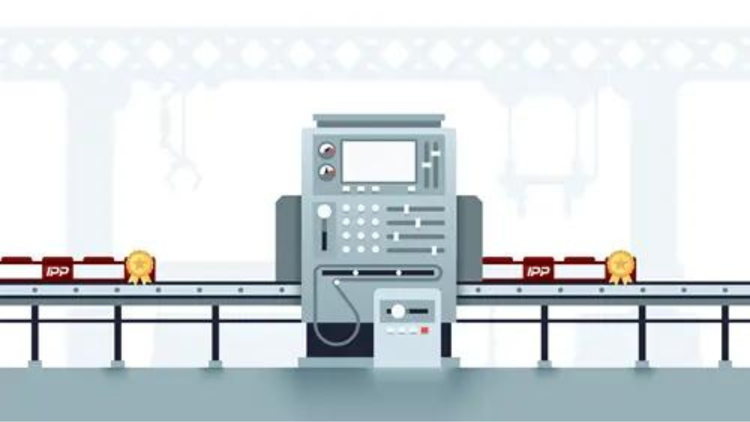